ドイツ本国 BMWライプツィヒ工場が電子部品生産の勢いを進めるなか、同工場でBMWグループ工場初のセル・コーティング・ラインが連続稼動を開始したことを発表。2024年までには既存のモジュール組立ライン2基に3基目が加わり、さらにセル・コーティング・ライン4基と高電圧バッテリー組立ライン2基が追加され、4つの塗布ラインは、年中におよそ2カ月間隔で連続稼働を開始するという。
1時間で2,000個以上のセルをコーティング
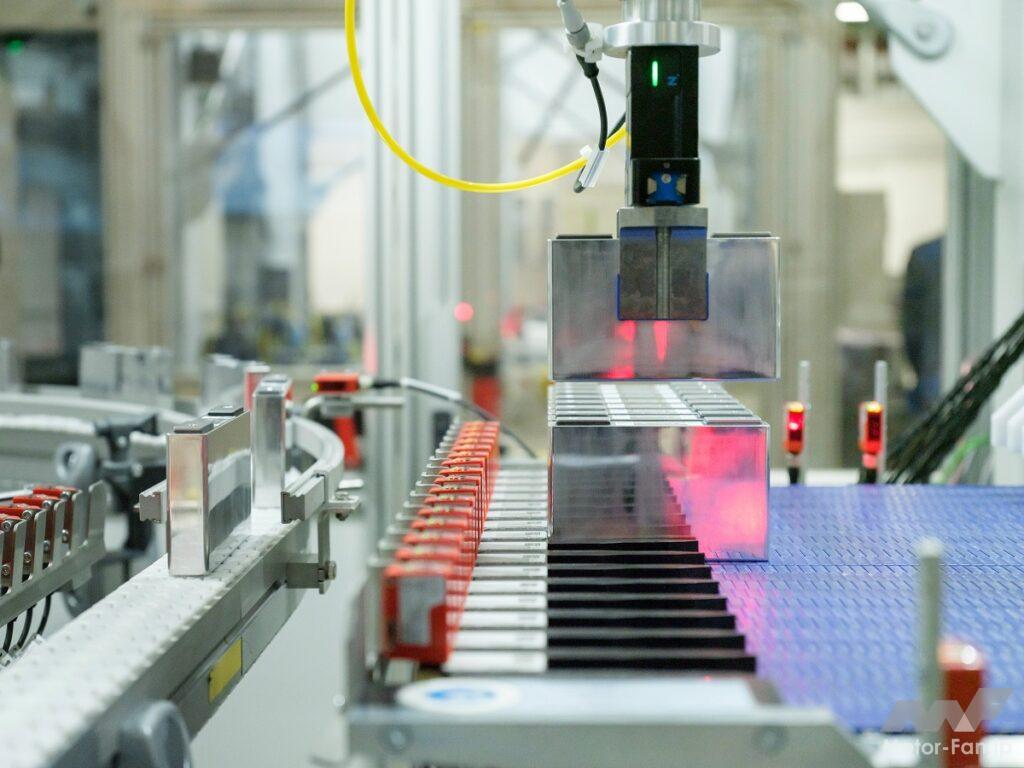
ライプツィヒのBMW工場にある新しいセルコーティングシステムの部門は、工場内で2,300m²の面積を占めている。同部門は、昨年夏に生産を終了したBMW i3の旧製造ホールに設置されており、バッテリーモジュール用セルコーティングの第1ラインが稼動開始。i3の生産終了後、わずか6ヶ月足らずで電子部品製造用に改造され、従業員も関連するトレーニングを受けている。
新しいコーティングラインは、年間1,000万個以上、1時間に2,300個以上のセルを処理することができる。コーティングされたセルは、ライプツィヒのバッテリー・モジュール生産ラインで使用され、完全電気自動車のBMW i4およびBMW iX1用のモジュールが生産される。同施設の別のラインでは、BMW iX用のバッテリー・モジュールが生産されている。
セル塗工から高電圧バッテリー生産まで
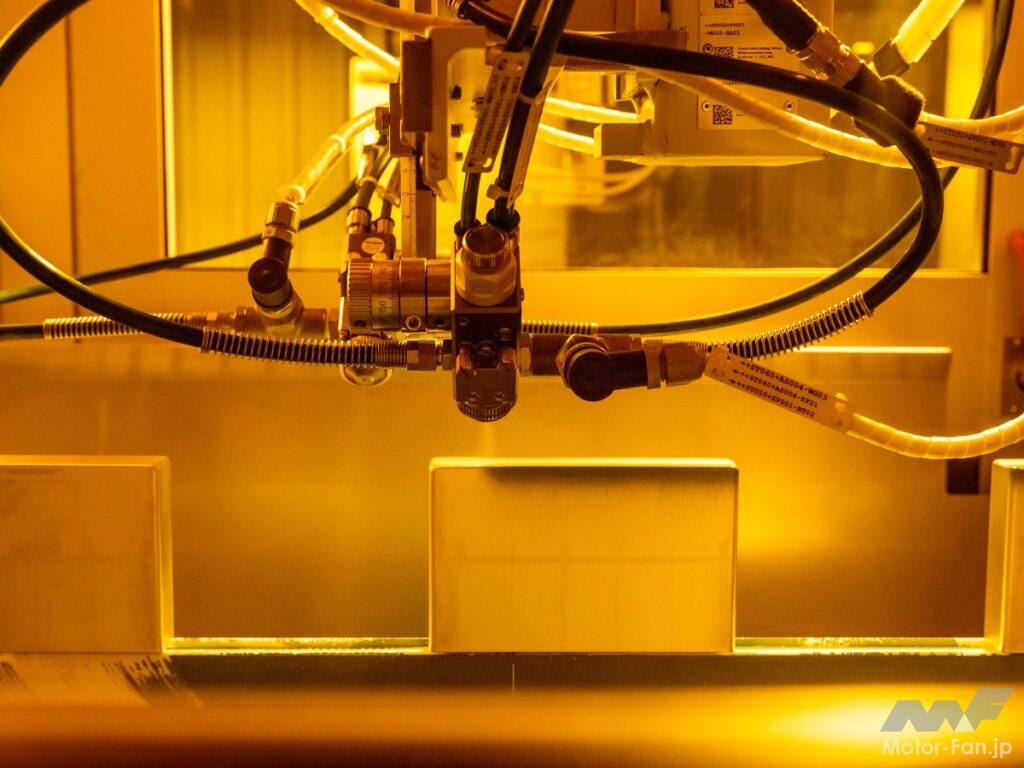
高電圧電池の生産は、セルの塗布、モジュールの生産、電池本体の組み立ての3つの工程で行われる。また、これらの工程は高度に自動化され、優れた生産能力を誇る。
リチウムイオン電池のコーティングは、まずレーザーで前処理が行われ、表面にパターンを形成することから開始する。これは、レーザービームがコーティングされていないセルの外側に “刻み “を入れて表面積を増やし、アルミニウムケーシングの表面張力を低下させるものである。続いて、セルに付着した汚れや酸化物を除去するプラズマ洗浄が行われる。この2つの工程を経て表面の密着性が向上し、コーティングの準備が整う。特別に開発された機械によって細胞を2層にコーティング、紫外線で硬化させることで、細胞に最適な絶縁性が実現される。最後に、全自動で3段階の品質管理が行われ、コーティングの厚みと表面品質が検査される。さらには、コーティングに欠陥がないことを確認するために、高電圧テストが実施される。
コーティングされたバッテリーセルは、モジュールと呼ばれる大きなユニットに組み上げられる。完成したモジュールは、制御装置や冷却装置、車両に接続するためのコネクターとともに、アルミニウム製のハウジングに収められる。筐体の大きさや形状、中に入れるモジュールの数は車種によって異なってくる。こうして、それぞれのクルマに最適な高電圧バッテリーが生産される。
ライプツィヒ工場の将来
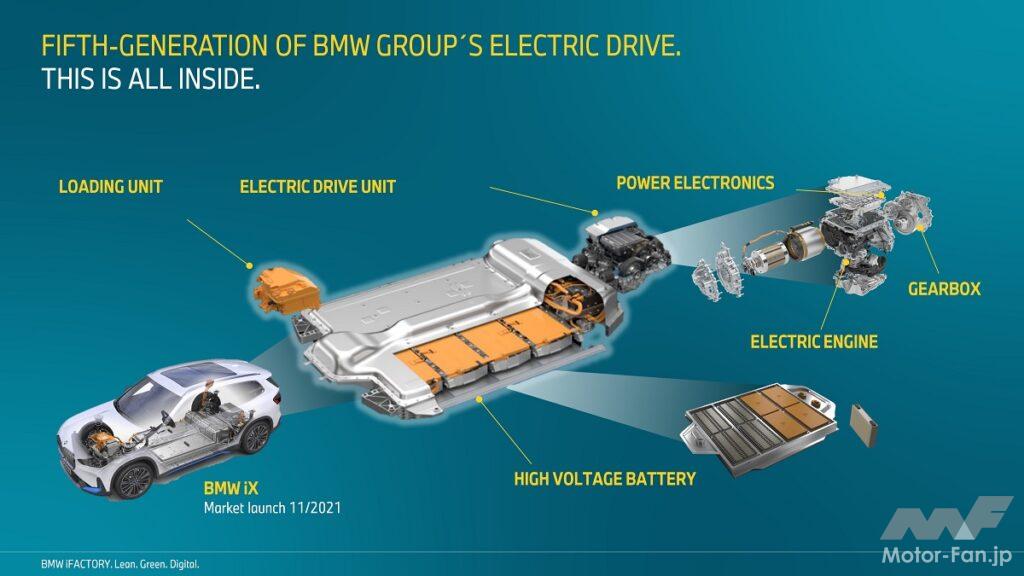
「ライプツィヒ工場の継続的な拡張は電子部品生産に大きく影響されています。将来的に、電子部品生産部門は、約15万m²の製造スペースを占めることになるでしょう。これはライプツィヒ工場の将来に対する長期的な投資なのです。」と、ライプツィヒ工場長のペトラ・ペーターヘンゼル氏は述べている。現在、電子部品生産ラインには、800人以上の従業員が従事しているが、2024年には1,000人以上に増加されるという。
ライプツィヒ工場にとって次の大きな節目は、MINIカントリーマンの後継モデルの生産であり、今年末には生産ラインから出荷される。このクロスオーバーには、燃焼式エンジンと、ライプツィヒ製の高電圧バッテリーを搭載した完全な電気駆動方式が用意される予定となっている。
からの記事と詳細 ( BMWグループのドイツ・ライプツィヒ工場で電子部品生産が拡大 - MotorFan[モーターファン] )
https://ift.tt/EXlL0bc
No comments:
Post a Comment